Shear Strength and Welding: What You Need to Know
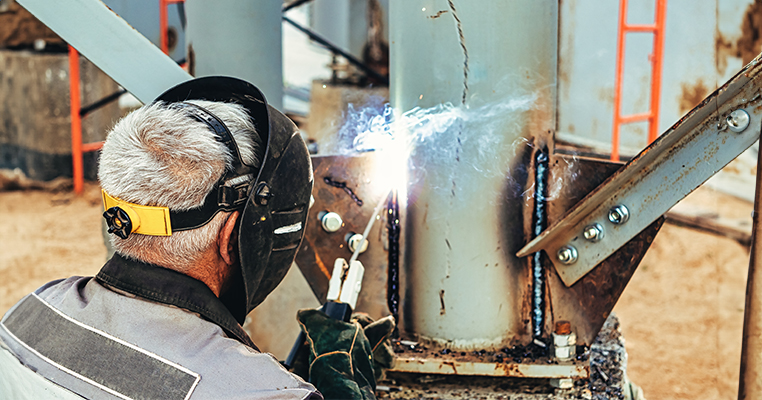
There’s no such thing as a perfect weld. Different kinds of welding and joints have different material properties.
Take, for example, a situation where you have two square tubes of steel, and you need to join them at a right angle. Do you:
- Put one flat end against the perpendicular surface of the other in a T joint.
- Put one next to the other and weld to the side?
- Adhere studs, drill holes, and use stud welding?
- Grind the ends into a 45-degree miter.
- Do you bevel the edges into a groove weld, or do you use a fillet weld on the surface?
Different means of attaching the materials to one another will have different properties and different strengths. Some will be better against twisting tension; others will be better against horizontal shear.
Shear strength is one of the most important kinds of strength for a weld to possess. In fact, since the shear force is the one most likely to break a weld joint – it’s the kind of stress welds are weakest – it’s an incredibly important consideration.
So, what exactly is shear strength in terms of welding, how can you calculate it, and how can you account for it in your welding?
What are Shear Stress and Strength?
Shear strength is defined as the ability of a material to resist forces that cause the material to slide against itself. When we’re talking about joining two materials, the shear force is the force that would slide the two materials along the axis of one of them.
Imagine a stack of books, one on top of another. If you press on one from the side, pushing it such that it slides cover across the cover to fall, this is a shear force. Shear force can be resisted in many ways; putting weight (or compressive force) downwards on the stack increases friction, making it require more shear force to “break” the stack. An adhesive like glue would join the books together and further inhibit shear forces.
Note: shear strength and shear stress are different. Shear stress is the force that applies to the material and is calculated based on the loads placed on the materials and the joint in question. Shear strength, meanwhile, is an inherent property of the material. Two identical pieces of steel will have the same shear strength but different resistance to shear stress depending on the joints they’re used in.
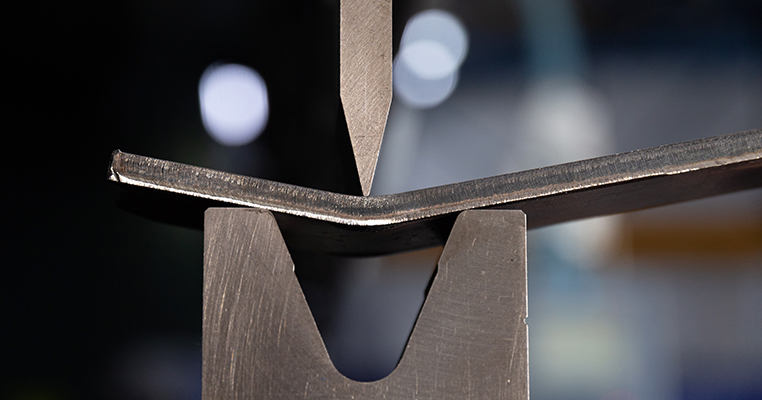
The same basic idea applies to welding. When you join two materials, various forces can apply to them, including to the joint. Some of those forces apply tension or torsion, some of them apply compression, some are ending, and some are shear.
The difference is that in metals that are fused together, it’s not shear forces applying between discrete objects like books (or metals); it’s applying between molecules.
Shear forces are important to resist primarily because the welding joint is a potential point of failure. It’s a fault line where metals have been melted, which can change their chemical and molecular properties. This is also why knowing whether or not a metal needs heat treating, choosing the right filler to melt and mix together, and ensuring proper depth of weld penetration are all critical.
This is also why, for example, porous welds full of impurities are bad. Those pores or impurities are weak areas that break the crystalline structure of the metal and, thus, can make the joint more susceptible to shear stress.
Sometimes, a joint is stronger than the material around it. This is common in woodworking, where wood glue forms a solid enough bond that the wood around it will break before the glue joint itself breaks. This can also be a concern when you’re welding certain metals.
How is Shear Strength Calculated?
Calculating the shear strength of a joint requires knowledge of a bunch of different factors. These include the size and shape of the weld, the type of joint, the materials, and even details about the tensile strength of the materials. Different parameters, including how thick the filler is, how thick the materials are, and whether or not the weld is sound, will all affect the end result.
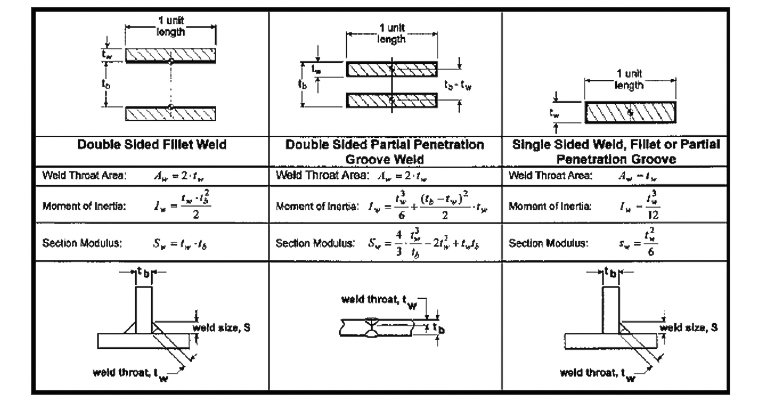
In other words, this isn’t simple napkin math but a complex element of materials science and engineering. Fortunately, most welders aren’t going to be making these calculations on the fly; they’ll have a combination of ingrained knowledge and assurances from the engineers who designed the weld that they’ll be structurally sound.
Factors that Matter to Shear Strength Calculations
When you consider calculating the shear strength of a weld, numerous factors matter.
- The size of the weld. The larger the weld is, the stronger it generally will be in proportion to that increase in size.
- The geometry of the weld. A weld with improper geometry will be weaker than it might seem to be when other factors are the same. This is why consistency across the length of a weld is important and why picking the right type of joint is critical for strong welds.
- The materials involved. The base materials have their own known shear strength based on what kind of metal they are. The filler material will also have a known shear strength when used in welding, and the combination of the two (and how they interact in a weld pool) is critical. It does you no good to make a weld using the wrong filler, failing to adhere the materials, and leaving a weak weld behind.
- Welding technique. The skill and technique used by the welder are important, as an improper weld can be inconsistent in geometry and penetration, as well as deposition and size. All of these can weaken a weld.
- Joint preparation. In particular, when a material is coated, rusty, or otherwise layered with something that can adulterate a weld, it matters. Welding, while hot, doesn’t just burn away these impurities; it forms pockets or impurities in the core material, can cause oxidation, and leave behind a poor-quality weld.
- Welding process. Certain processes can be considered stronger than others. Most people consider TIG welding to be stronger than MIG or stick, predominantly because the process itself allows for better deposition, better penetration, less chance of inconsistent welding, and more.
- Type of joint. As mentioned above, a simple tee joint with a fillet weld is going to have different material properties than a bevelled joint, a stud weld, a butt joint, and other kinds of joints. In fact, many of these alternative styles of welding were developed specifically to improve the shear strength of the resulting joints.
As you can see, there are many considerations in play.
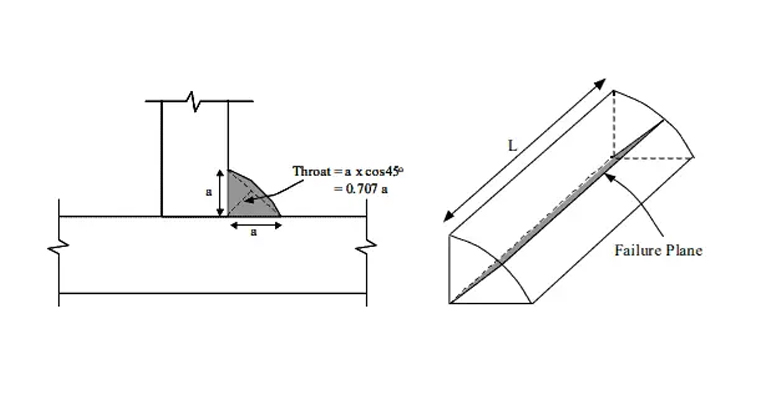
One of the simplest possible weld joints to use as an example is a tee joint using a fillet weld with no beveling, no additional preparation, the same materials and thickness, and other details controlled for. A basic calculation is this:
Shear Strength = 0.707 x Weld Throat x Weld Length x (Tensile Strength/3). ( source )
The throat is the depth of the fillet weld’s bead. This can be calculated by measuring the coverage depth of the bead and calculating the depth at the middle angle. To put it more generically:
Shear Strength = Weld Size x Weld Length x Allowable Shear Stress
The weld size is the distance between the joint’s root and the outer edge of the weld. This is close to, but not exactly, the throat length; however, it’s measurable on the fly and much easier to estimate and use in calculations than the throat size of the same weld. Weld size can, of course, be adjusted by using multiple passes for the weld and depositing more material.
The weld length is the total length of the weld along the joint. Longer welds are generally stronger welds because there’s more material and more “surface area” to prevent the material from breaking under shear forces.
Allowable shear stress is the force expressed in a measurement like PSI that depends on the material, design of the weld, and industry standards.
What Kinds of Welds are Strongest?
When considering how strong a weld is, there are many considerations that affect the answer. Unfortunately, there’s no clear “this is the best” weld or joint; it all depends.
The most important considerations are the materials, the purpose, and the design of the weld joint.
The materials have a significant impact on the strength of a joint. This is why making a building out of wood versus making one out of steel is a real consideration. Houses, which aren’t subject to extreme forces in general, can be made of wood; skyscrapers, which have much more force acting on them, use steel for structure. Each individual connection in a massive building may be a weld, a rivet, or a combination, and they are all designed for that strength and the forces acting on the building.

The purpose of the weld joint is also important because it defines what kinds of forces the joint will have to resist. Imagine a table. The surface is supported by legs attached to the bottom. There’s no real shear strength in the vertical direction, which is where the majority of the force on the table will come from. Shear strength would be horizontal forces, which are atypical for a table.
But, if you flip the table on its side and put vertical pressure on the legs, you have two kinds of stress acting on them: shear and bending. This is the same structure, physically, as a cantilever . These joints, to be supportive, need to resist these forces to a higher degree than in the other orientation.
The design of the joint is also critical. Butt joints, tee joints, corner joints, lap joints, edge joints; they all have different pros and cons when it comes to the forces they can resist and the forces that are more likely to break them.
All of this goes back to the very first question we asked at the start. How would you design such a joint? Answering that question has cascading effects on the rest of the process.
Ensuring the Strongest Possible Welds
Ensuring the strongest possible joint means making sure every factor that goes into the strength of the joint is skewed in your favor.
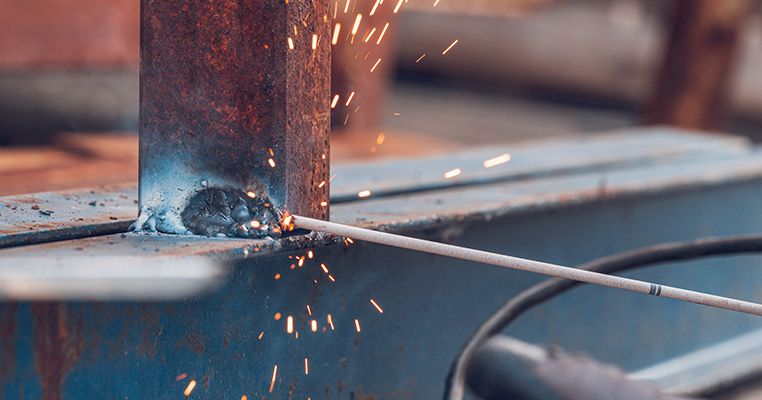
Designing the weld is the engineer’s task. Picking the right materials is the designer’s task. Understanding the overall loads and construction, again, falls on the engineer. At the ground level, as a welder, you have more specific concerns.
- Make sure you’re following any welding specifications precisely. Cutting corners weakens welds and makes them more susceptible to various forces, including shear.
- Use the right filler material. Fillers with high ductility are generally stronger against shear stress because they can deform slightly without snapping, whereas brittle materials will break, often suddenly.
- Use a fast, consistent process. Something like TIG allows for a minimal amount of heat-affected material, which avoids weakening parts of the material that aren’t then reinforced as part of the weld pool.
- Use consistent speeds, deposition rates, and travel rates. Consistency is critical because any area where there’s variability means a weakness or disparity in the overall strength of the joint.
Something that can help with almost all of these factors is the overall quality of the welding machine you’re using. A good, high-quality machine will input consistent current and allow you to use modern technologies like pulsed current, which can ensure high-quality welds while reducing the heat put into a workpiece. They can also have a variety of useful features to help ensure consistent welds, including automatic deposition adjustments, current adjustments, and even welding automation.
So, if you’re on the lookout for a high-quality tool to help you ensure that you produce high-quality welds, look no further. At Red-D-Arc, our welding equipment rentals can do all of that and more. You can find excellent machines for individual welders, all the way up to fully automated and robotic systems, alone or in bulk. Whatever your needs, we have something that can help. All you need to do is reach out to talk about your needs or browse our catalog to see what’s on offer.
Related Posts:
Red-D-Arc, an Airgas company, rents and leases welders, welding positioners, welding-related equipment, and electric power generators – anywhere in the world. Our rental welders, positioners and specialty products have been engineered and built to provide Extreme-Duty™ performance and reliability in even the harshest environments, and are available through over 70 Red-D-Arc Service Centers, strategically located throughout the United States, Canada, the United Kingdom, France, and the Netherlands, as well as through strategic alliances in the Middle East, Spain, Italy, Croatia, and the Caribbean. From our rental fleet of over 60,000 welders, 3,700 weld positioners, and 3,700 electric-power generators, we can supply you with the equipment you need – where you need it – when you need it.
Share this
| Print this
Categories
- Aluminum Welding
- Blast Cleaning
- BotX Welding Cobot
- Company News
- Conferences & Shows
- COVID-19
- Customer Applications
- Dry Ice Blasting
- Emergency Power
- Generators
- Hypertherm
- Induction Heating
- Industrial Generator
- Industry News
- Lincoln Electric
- MIG Welding Equipment
- Miller Electric
- Pipe Welding and Cutting
- Plasma Cutters
- Plasma Cutting
- Product News
- Promotions
- Rental Equipment Brands
- Renting Generators
- Renting Welders
- Robotics
- Safety
- Specialty Equipment
- TIG Welding Equipment
- Weld Automation
- Welding
- Welding Fume Extractors
- Wet Media Blasting
Archive
- 2024 (58)
- September (1)
- Webinar: 3 Options for Fabricators to Scale Welding Capacity
- Maximizing Efficiency in Metal Fabrication with Dry Ice Blasting
- Visit Us and Shop for Savings on Used Welding Equipment
- Visit Us and Shop for Savings on Used Welding Equipment
- It's the Season for Unpredictable Conditions: Are You Ready?
- AWS Welding Summit 2024: Making an Impact on the Welding Industry
- Video: Red-D-Arc Automation Equipment — Positioners, Manipulators and Turning Rolls
- Collaborative Efforts to Improve Welding Processes Leads to Transformation for MWI Pumps
- Lease the Ranger® Air 260MPX™ Multi-Function Engine Drive from Red-D-Arc
- What to Look for in Welding Helmets: Comfort, Safety & More
- Guide: What is Weathering Steel and How Do You Weld It?
- Video: Red-D-Arc Port-A-Weld System (PWS)
- FABTECH Canada 2024: Shaping the Future of Manufacturing
- FAQ: How Do You Eliminate Corrosion in Steel and Aluminum?
- The Rise of Prefabrication in Construction
- How to Set Up a Space to Weld Safely in Your Workshop
- Guide: How a Material's Melting Point Can Affect Your Welds
- Multipass Welding: Techniques, Number of Passes & Benefits
- Join Us: Dry Ice Blasting and Orbital Welding Equipment Demonstrations
- Induction Heating Equipment Available for Rent, Lease and Purchase
- Red-D-Arc Offered a Look at its Portfolio of Welding Equipment, Expertise at SEAA 2024 Convention & Trade Show
- National Welding Month Spotlight with Brian Imhulse
- Equipment Spotlight: Used Generators & Distribution Equipment for Sale
- Red-D-Arc Expert Highlight: Meet Tim McCurry, CWS
- Don’t Miss Our Spring Used Welding Equipment Sales
- Video Tutorials: AXXAIR Orbital Welding Equipment
- LB Construction Boosts Productivity with the Red-D-Arc Logistics Lease Program
- The Difference Between Forehand vs Backhand MIG Welding
- The Differences Between Welding, Brazing and Soldering
- The Role of Submerged Arc Welding in Heavy Fabrication
- Dry Ice Blasting Effective for Sanitizing Microbial Contamination
- Beyond the Weld: Quality Assurance in Pressure Vessel Welding
- Welding Cast Metals: Cast Iron, Cast Steel & More
- Preheating in Welding: When and Why Is It Necessary?
- Underwater Welding: Challenges, Techniques, and Safety Tips
- Welding Speeds: Distortion, Stress, and Recommendations
- Industrial Disaster Remediation with Dry Ice Blasting
- Welding Protocols and Quality Assurance in Aerospace Construction
- Navigating Challenges: Welding in Aerospace Materials
- The Art of Welding Thin Materials: Techniques and Tips
- Laser Cutting vs. Plasma Cutting: A Complete Comparison
- Preheat Steel for Structural Welding More Efficiently and Safely with Induction Heating
- Welding Integrity: Ensuring Safety in Petrochemical Facilities
- Automating the Pipe Welding Process
- The Role of Welding in Aerospace Manufacturing
- Scratch-Start, HF, and Lift-Arc: Pros and Cons, Safety & More
- Red-D-Arc Supports Local Eagle Scout Project
- 2024 Winter Fancy Food Show: Get a Taste of the Food Industry’s Best
- Advantages of Dry Ice Blasting vs. Traditional Cleaning Methods
- Miller® Big Blue® 400 Pro
- Don’t Miss Out: Save on Used Welding Equipment
- What is Hardfacing in Welding and How Can You Apply It?
- BotX™ Helps Improve Welding Cycle Time at Estes Design and Manufacturing
- Garrison Steel Maximizes Uptime with Red-D-Arc’s Logistics Lease Program
- Choosing the Right Size Generator Rental for Your Emergency Power Needs
- Precision and Power: Advanced Welding Processes
- Lincoln® Dual Maverick® 200/200X
- Plasma Cutting Power Requirements by Metal Thickness
- December (5)
- Welding For Oil Refineries and Gas Processing Facilities
- Shear Strength and Welding: What You Need to Know
- How to Optimize Workflow with Multi-Process Welding Equipment
- From Blueprint to Maiden Voyage: Welding's Integral Role in Shipbuilding Projects
- How to Weld Cast Iron: MIG, TIG, Stick, and Arc Welding
- Ensuring Structural Integrity: The Critical Role of Welding in Offshore Platform Construction
- TIG Welding Stainless Steel: Best Practices and Common Pitfalls
- How to Reduce Wear and Tear on Your Plasma Cutter
- The Fine Art of Fusion: Exploring TIG Welding Without Filler Metal
- Corrosion Control and Welding in Offshore Environments: Strategies for Longevity
- Welding Alloys for Petrochemical Applications: Selecting the Right Materials for the Job
- The Environmental Impact: Sustainable Welding Practices in Industry
- Analyzing the Efficiency of Portable vs. Stationary Fume Extractors
- Welding Inspection and Quality Control: Ensuring Excellence in Mechanical Contracting Welds
- Submerged Arc Systems Increase Productivity by 250%
- Tips for Mechanical Contractors: Choosing the Right Welding Equipment for Your Projects
- Avoid Downtime: Proper Maintenance Tips for TIG Welders
- The Role of Welding in Maintenance and Repair of Petrochemical Facilities
- Don’t Miss This: Big Savings on Used Welding Equipment
- The Future of Welding Automation
- SEMA Show 2023: Connecting with the Automotive Industry
- Now Available at Red-D-Arc: Axxair SATFX-170 Welding Head
- Tank Manufacturing Made Easy with Weld Automation Equipment
- Lincoln Electric Frontier® 400X
- Welding for the Long Haul: Ensuring Durability and Reliability in Pipeline Construction
- Power Generators: Should You Rent or Purchase?
- Red-D-Arc Induction Heating Solutions
- Nu-Ice COMMANDO® 55 Dry Ice Blaster
- BotX™ Helps JJJ Container Services Address the Skilled Welder Shortage
- Elevate Your Welding Game with Miller's Generator Welders
- Welding Positions and Joint Types: 1G, 2G, 3G, 4G, 5G, and 6G
- How Does a Plasma Cutter Work? Parts, Process & More
- How Do You Reduce Work Noise When Welding and Cutting?
- Safety Considerations For Welding Indoors and in Enclosed Spaces
- FAQ: How Does Plasma Cutting Compare to Waterjet Cutting?
- Oxy-Acetylene vs. Arc Welding: Cost, Safety, and Usage
- The Two TIG Welding Polarity Types: Reverse and Straight
- How to Choose the Right Flux-Core Aluminum Welding Wire
- The Official Guide to Different Welding Processes
- Don’t Miss Out: Save on Used Welding Equipment
- FABTECH 2023: Driving Manufacturing Forward
- Welding Rod Types: What Are They and Their Various Uses?
- Stud Welding in the Shipbuilding Industry
- How To Reduce Dross and Slag During Plasma Cutting
- Stud Welding Applications
- Miller’s Pipeworx Welding System
- Mig vs. Pulsed Mig vs. Doubled Pulsed: What's The Difference?
- Advantages Offered by Plasma Cutting
- Be Prepared: How to Create a Power Outage Contingency Plan
- Training Experts to Serve the Welding Industry
- 6 Essential Tips for Hurricane Preparedness for Businesses
- Welding in the Oil and Gas Industry
- Applications of Flux-Cored Welding
- Flux Core Wire Types
- Pipeline Welding Equipment
- The Ultimate Guide to Welding Blankets: Safety, Selection & More
- Offshore Welding Equipment Requirements
- BotX™ Demo Days are Back
- Dry Ice Blasting for Robotics, Weld Lines and Fixturing
- Lori Kuiper Featured on Arc Junkies
- Limited Time Only Offer: Welding Equipment Packages
- Viper and Python SYNC series plasma cutters
- Benefits of Lincoln Electric Advanced Welding Technologies
- The Benefits of Miller’s Suitcase Wire Feeders
- Weld Aluminum with a MIG Welder
- Can You MIG Weld Mild Steel to Stainless Steel
- 12 Tips and Tricks for Welding Magnesium-Based Alloys
- Benefits of Lincoln MIG Welders
- Different Types of Miller TIG Welders
- The Different Types of Stud Welder Systems and Stud Guns
- Types of Lincoln Wire Feeders
- December (6)
- Labor Shortages in Welding: Is There a Solution?
- Can you stick weld with a TIG welder
- Common Industry Applications of MIG Welding
- Most Commonly Used Hardness Testing Scales for Welding
- The Beginner's Guide to Welding Positioners and How They Work
- The Benefits of Hypertherm's Powermax SYNC Technology
- Mig Welding for Beginners: Can You Mig Weld Aluminum?
- Flux-core Welding and Stick Welding: What's The Difference?
- Corner Joint Welds: Types, Procedures, Tips & More
- The Beginner's Guide to Welding a Tee Joint (With Tips)
- Dry Ice Blast Cleaning Provides Environmentally Friendly Solution for Refinery Emergency Shutdown Heat Exchanger Cleaning
- Weld Summit 2022 – Houston
- Come Join Us at FABTECH Atlanta
- Generator Paralleling Delivers Increased Fuel Savings Compared to Single-Unit Operation
- Miller’s Latest Dynasty TIG Welders Now Available for Rent and Lease
- AWS Welding Summit 2022
- Steel-Aluminum Welding: Issues and Work-Arounds
- Welding Automation: Arc Motion vs Work Motion
- Tools that Improve Pipe Welding Efficiency
- Rent the Right Generator
- The Welding Equipment Used in Automotive Shops
- The Advantages of Inverter Welders
- TIG Welding Aluminum
- The benefits of using an engine-driven welder generator
- Induction Heating Applications for Welding and Industrial Maintenance
- Lincoln's Dual Maverick Diesel Engine Driven Welder
- Cutting Aluminum with a Plasma Cutter
- Tools To Use For Flux Core Welding
- Aluminum Welding: Challenges and Considerations
- Welding Rental for Beginners: Which Type of Welder Should I Rent?
- Choosing the Right Welding Method When Renting a Welder
- MIG vs TIG Welding: Which Method Is Right for Your Application?
- New BotX Integration Facility Opens, Announcing New BotX Team Members
- Upgrades to our Tier-4 Final Generator Fleet with New ComAmp and Deep Sea Electronics PLC Controllers
- TIG Welding with Red-D-Arc's GX330XL Portable Gas Welder
- December (1)
- Dry Ice Blasting Advantages Over Other Cleaning Methods
- Sourcing Welding Equipment During Supply Chain Interruptions
- Introducing Red-D-Wraps - Adaptable Induction Heating Wraps
- How Welding Automation Can Bridge the Skill Gap in the Manufacturing Industry
- What Are Customers Saying About BotX?
- Full-Featured Spool Gun for Pulse Aluminum Welding (GMAW-P) with Red-D-Arc’s New GX330XL Portable Gas Drive Welder
- Steel Erectors 48th Convention Trade Show 2021
- Robots vs. Cobots: What's the Difference?
- Emergency Power Generators - It Pays to Plan Ahead
- How a TIG Welder Can Extend The Life of Aircraft Parts
- BotX Robotic Welder Feature Article on Automation.com
- BotX Welding Cobot: Radial Weld Set-Up Challenge
- Flood Response: 300 kVA Generators Onsite in the Bayou
- Welding Cobot Solves Production Challenge for Ontario Auto Parts Manufacturer
- How to Choose a Generator
- Welding Aluminum Just Got Easier with the Lincoln Magnum SG
- The Lincoln Dual Maverick Gives Twice the Power
- The Arc Reach Heater Makes On-Site Heat Treatment Fast and Easy
- Costs of a Generator Rental in 2021
- What is the Welding Cobot Advantage?
- Supporting Community Development in Vancouver BC
- How To Choose the Right Industrial Generator Rental
- What Are The Factors To Consider With a Generator Rental?
- December (1)
- Dry Ice Blasting for Industrial Paint Booth Cleaning
- Webinar - Manufacturing: The Next Generation
- Benefits of Renting Equipment During A Pandemic
- 27 Minute Coupling Hub Removal
- Proper Maintenance of Power Generators
- 17,000 Square Ft. Gymnasium Ceiling Renewal
- Seized Blow-Out Preventer Un-Stuck After 9 Years
- Unraveling the Mystery of Heat Treatment
- Storage Tank Fabricators Build Efficiently with Induction Heating
- OVER 100 GENERATORS TO PROVIDE TEMPORARY POWER FOLLOWING HURRICANE LAURA
- How Can Power Plants Manage the Challenges of Seasonal Heat and Outages
- Microgrids Deployed Today - Filling the Void Within the Electric Utility Infrastructure
- Hurricane Season? Here Are Five Important Standby Tips to Consider
- 10 Ways to Reduce Costs and Boost Productivity with TIG Welders
- Welding in the Construction Industry
- Innovative Solutions In a Time of Crisis
- 6 Ways Welding Factors Into Successful Plant Shutdowns
- Post-Processing Welded Parts
- COVID-19 Update
- Welding Aluminum To Steel
- Dry Ice Blasting for Statue Restoration and Quality Preservation
- December (1)
- Welding Quality Assurance & Quality Control Processes
- Plant Maintenance in the Coatings Industry
- Dry Ice Blasting Provides Speedy Restoration for University
- Our Beaumont TX Branch Has Moved
- Choosing The Right Welder For Building a BBQ Smoker
- New Welder Technology: ArcReach Technology
- How Does the Clearblast 150 Wet Media Blaster Work?
- What are the differences between types of tungsten electrodes?
- 9 Tips to Help Prevent Wire Feed Problems in MIG Welders and Flux-Cored Welding
- Top 3 Advantages of Using Pulsed-MIG Welders
- Features of the Millermatic 252
- 6 Tips to Improve Welding Safety
- Different Welding Certifications
- Supporting Maintenance at the Grand Coulee Dam
- Construction Firm Beats Competition With Fast Induction Heating
- Plasma Cutting Equipment Selection & Process Safety
- Benefits of Welding Equipment Rental
- Comparing Welding Equipment Rentals
- Induction Heating vs Other Methods
- Welder shortage: Key is efficiency, not automation
- Multi-Process Welders
- Stud Welders
- November (1)
- Dry Ice Blasting Applications in the Oil and Gas Industry
- Complications with Burning Biodiesel in Modern Diesel Engines
- Axxair Orbital System Makes Welding Small Pipes Easy
- New Product Offering: Adjustable Pipe Stands
- What Do American Welding Society Wire Filler Metal Designations Mean?
- 92% Improvement - Turning Problems into Possibilities with a Custom Welding Package
- Emergency Generators Provide Power for Oregon Firefighters
- Naval Defense Contractor Builds Smarter with Leasing
- Come See Us at Fabtech Canada 2018 - Booth #1381
- Red-D-Arc Atlanta Receives ISO 9001 2015 Certification
- The Red-D-Arc Smokin-Welders Win Big at the ABC Gulf Coast Cookoff
- Dry Ice Blasting Paint Booth Rental Package
- Strengthening Metal Parts with Hardfacing
- Is Gas Welding Really Cheaper?
- Overview of Tier III and Tier IV Diesel Emissions Standards
- We're at the Pipeline Energy Expo in Tulsa
- The Importance of Welding Surface Preparation
- Preheating Applications in Welding
- Power Generator Rental for Concert in Timmins, Ontario
- Smoke Extractors: Remove Fumes and Add Value
- Red-D-Arc Feature in Tank Storage Magazine
- Fast, Efficient Flux-Cored Welding with Semi-Automatic Wirefeeders
- November (3)
- Welding Equipment Assists With Offshore Wind Farm Projects
- Producing High Quality Welds in Stainless Steel Welding
- Dry Ice Blasting - Save Money, Reduce Waste and Increase Efficiency
- Red-D-Arc Turnkey Packages Support the World's Largest Offshore Wind Farm
- Naval Shipyard Welding: Air Arc Gouging Saves the Navy Time and Money
- Keeping Quality High in Pipe Welding Applications
- The 5 Most Common Mistakes Found by Welding Inspectors
- Pipe Welding Equipment
- New Red-D-Arc Branch in Regina, Saskatchewan
- Red-D-Arc Company Overview Video
- Efficient Pipe Welding with the Red-D-Arc Process Pipe Cell
- Induction Heating Speeds up Repair of the World's Largest Rock Crusher
- December (1)
- Red-D-Arc Equipment Available at Select Air Liquide Branches
- Lease Your Core Fleet of Welding Equipment
- International Pipeline Conference & Expo
- Customer Project: Tesla Gigafactory
- Steel Fabrication Company Lowers Costs, Increases Productivity
- Orbital Welding in Opelika: Demo of Orbitalum's powerful pipe welder
- Apex 2100 Orbital TIG Welding System Demonstration
- Quick Response Helps Flood Recovery Efforts
- Having a Blast in the Lions Den
- Texas Welding Training Institute Expands by Leasing Welder Certification Trailers
- Customer Project: Minnesota Vikings' New Stadium
- Customer Success Story - Pierce Metals
- Featured Product: E.H. Wachs Guillotine Pipe Saws
- Farrow 150 Wet Abrasive Blasting System
- Offshore Technology Conference 2016 | Red-D-Arc Booth #423
- Red-D-Arc 30 ft Boom Manipulator
- Lions, Sharks and . Dry Ice Blasting?
- 44th Annual SEAA Convention & Trade Show
- Extending the Legs of a Large Seabound Work Platform
- Submerged Arc Systems for Wind Farm Manufacturing
- Induction Heating Used for Removal of Hydroelectric Generator Rotor
- Red-D-Arc Installs Cladding System in Qatar
- Spring Deals on Used Welding Equipment: April 1-June 30th
- Red-D-Arc Installs Weld Overlay Cladding Facility in Scotland
- Red-D-Arc Offers the Latest Dry Ice Blasting Technology
- Red-D-Arc’s Bidadoo.com Online Auction Ends Thursday March 10th
- Growing Line Systems Used for Wind Farm in Adriatic Sea
- Red-D-Arc Works on The Wilshire Grand Centre
- Send Us Your Story - Get a Free Hat
- Featured Product: Millermatic 252 - The welder that you can teach anyone to weld with
- Red-D-Arc Social Media
- Winter Deals on Used Welding Equipment: January 1 - March 31
- December (3)
- Red-D-Arc Supports Grimsby Welding Program
- Red-D-Arc Generators to Power Niagara Wind Project
- Mobile Lighting Towers Now Available
- Red-D-Arc Elevating Head and Tailstock Positioner - RDA EHTS200 NA
- Red-D-Arc Blasterentals Keeps the Fleet Rolling at Smith Transport
- See us at FABTECH 2015 in Chicago
- MacAljon Increases Thin-Wall Tank Productivity by Over 50%
- Airgas/Red-D-Arc’s Weld Efficiency Analysis
- Global Welding Equipment Market 2015-2019
- D&D Power Oilfield Services
- Sub Arc Welding Heads and Controls
- Red-D-Arc's National Accounts Program
- Visit Red-D-Arc at Insights 2015
- Farrow 150 Wet Abrasive Blasting System
- Free Welding Electrode Classifications Quick Reference Wallchart
- Turnkey Weld Automation Packages
- The Importance of Smoke Extractors
- Rent, Lease or Own Welding Equipment?
- Manufacturers Series Positioners
- Modular Fit Up Bed System for Thin Wall Cans